تفاوت آهن اسفنجی و گندله: مزایا، معایب و کاربردها
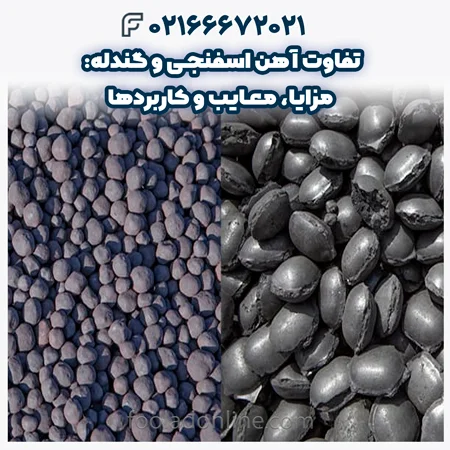
آهن اسفنجی و گندله دو ماده اولیه مهم در صنعت فولاد هستند که در فرآیندهای مختلف تولید فولاد استفاده میشوند. هر یک از این مواد ویژگیها و کاربردهای خاص خود را دارند که تفاوتهای مهمی بین آنها وجود دارد. در این بخش، به بررسی کلی تفاوت آهن اسفنجی و گندله پرداخته و نحوه تولید، نسبت تبدیل گندله به آهن اسفنجی و کاربردهای آنها را شرح خواهیم داد.
آهن اسفنجی (Direct Reduced Iron یا DRI) محصولی است که از احیای مستقیم سنگ آهن به دست میآید. در این فرآیند، سنگ آهن به کمک گازهای احیایی مانند هیدروژن و مونوکسید کربن به آهن خالص تبدیل میشود. آهن اسفنجی به دلیل خلوص بالا و ویژگیهای خاص خود، یکی از مواد کلیدی در تولید فولاد به شمار میآید. این محصول به صورت تودههای دانهای یا دانههای فشرده شده تولید میشود و به عنوان ماده اولیه در کورههای الکتریکی فولادسازی مورد استفاده قرار میگیرد.
گندله (Pellet) نیز محصولی است که از فرآیند تبدیل سنگ آهن به قطعات کوچک گرد یا گرانولهای فشرده شده به دست میآید. در این فرآیند، سنگ آهن با استفاده از مواد افزودنی و تحت فشار و حرارت بالا به شکل گندلههای کوچک درمیآید. این گندلهها به دلیل اندازه یکنواخت و خواص فیزیکی مطلوب، به راحتی در کورههای بلند استفاده میشوند و به عنوان ماده اولیه در تولید فولاد به کار میروند.
فرآیند تولید آهن اسفنجی و گندله
در این بخش، به بررسی فرآیندهای تولید آهن اسفنجی و گندله میپردازیم و تفاوت آهن اسفنجی و گندله را بررسی خواهیم کرد.
فرآیند تولید آهن اسفنجی
سنگ آهن ابتدا به اندازههای کوچکتر خرد میشود و سپس در مرحله آمادهسازی به صورت دانههای یکنواخت در میآید.فرآیند احیای مستقیم (Direct Reduction) برای تولید آهن اسفنجی استفاده میشود. در این فرآیند، سنگ آهن خرد شده با استفاده از گازهای احیایی مانند هیدروژن یا مونوکسید کربن در دماهای بالا (حدود 800 تا 1000 درجه سانتیگراد) واکنش داده و به آهن خالص تبدیل میشود. این فرآیند به دو روش اصلی انجام میشود: گازهای احیایی از پایین به سمت بالا در جریان هستند و سنگ آهن از بالا به سمت پایین میآید. گازهای احیایی از کنار کوره به سمت سنگ آهن ارسال میشود.پس از احیای مستقیم، محصول به صورت تودههای اسفنجی آهن که حاوی 90 تا 94 درصد آهن هستند، به دست میآید. این تودهها به صورت دانههای ریز یا بزرگ، بسته به نیاز تولید فولاد، آماده استفاده در کورههای الکتریکی فولادسازی میشوند.
فرآیند تولید گندله
سنگ آهن به قطعات کوچکتر خرد شده و سپس با استفاده از ماشینآلات مختلف به صورت پودر در میآید.پودر سنگ آهن با مواد افزودنی مانند بنتونیت (به عنوان چسب) مخلوط میشود. این مخلوط به شکل گندلههای کروی با قطرهای مختلف (معمولاً 8 تا 16 میلیمتر) در میآید. برای این کار از دستگاههای گلولهساز استفاده میشود. گندلههای خام تولید شده به کورههای پخت (گرمازا) منتقل میشوند، جایی که تحت حرارت بالا (معمولاً در دماهای 1200 تا 1300 درجه سانتیگراد) قرار میگیرند. این حرارت باعث میشود که گندلهها سخت شده و استحکام و کیفیت آنها افزایش یابد.پس از پخت، گندلهها آماده استفاده در کورههای بلند هستند. این گندلهها به دلیل یکنواختی و خواص فیزیکی مطلوب، به راحتی در فرآیند تولید فولاد ذوب شده و به کیفیت بالای فولاد کمک میکنند.
تفاوتهای اصلی در فرآیند تولید
- مواد اولیه: آهن اسفنجی از سنگ آهن به طور مستقیم و با استفاده از گازهای احیایی تولید میشود، در حالی که گندله از پودر سنگ آهن و مواد افزودنی به شکل گندلههای کروی تولید میشود.
- فرآیندهای حرارتی: در تولید آهن اسفنجی، فرآیند احیای مستقیم در دماهای نسبتا پایینتری انجام میشود، در حالی که گندلهها تحت حرارت بالا در کورههای پخت قرار میگیرند.
- شکل و خواص نهایی: آهن اسفنجی به صورت تودههای دانهای یا فشرده شده تولید میشود، در حالی که گندلهها به صورت گرانولهای کروی تولید میشوند که خواص فیزیکی و حرارتی متفاوتی دارند.
این فرآیندهای تولید، تأثیر زیادی بر ویژگیها و کاربردهای نهایی آهن اسفنجی و گندله در صنعت فولاد دارند. در ادامه مقاله، به بررسی دقیقتر تفاوتهای بین این دو ماده و کاربردهای آنها خواهیم پرداخت.
مقایسه خواص فیزیکی و شیمیایی
در این بخش، به مقایسه این خواص خواهیم پرداخت تا درک بهتری از ویژگیهای هر یک به دست آوریم و نحوه تأثیر آنها بر فرآیند تولید فولاد را بررسی کنیم.
خواص فیزیکی
- آهن اسفنجی: آهن اسفنجی به صورت تودههای دانهای یا گلولههای فشرده شده تولید میشود. اندازه این دانهها معمولاً متغیر است، ولی به طور کلی، آهن اسفنجی به صورت تودههای نسبتا بزرگتر و کمتر یکنواختتر نسبت به گندله در میآید.آهن اسفنجی دارای چگالی بالاتری است، که معمولاً در حدود 4 تا 5 گرم بر سانتیمتر مکعب میباشد. این چگالی بالا به دلیل درصد بالای آهن خالص در این ماده است. آهن اسفنجی معمولاً نرمتر از گندله است و شکنندگی کمتری دارد. این ویژگی به آن کمک میکند تا به راحتی در فرآیند ذوب در کورههای الکتریکی استفاده شود.
- گندله: گندلهها به صورت گرانولهای کروی یا دانههای کوچک و یکنواخت تولید میشوند. اندازه این گندلهها معمولاً در محدوده 8 تا 16 میلیمتر است، که باعث یکنواختی در فرآیند ذوب میشود. گندلهها دارای چگالی کمتری نسبت به آهن اسفنجی هستند و معمولاً در حدود 3 تا 4 گرم بر سانتیمتر مکعب قرار دارند. این ویژگی به دلیل درصد پایینتر آهن خالص و وجود مواد افزودنی در آنهاست. گندلهها سختتر از آهن اسفنجی هستند و به دلیل فرآیند پخت، مقاومت بیشتری در برابر شکستن دارند. این سختی به آنها کمک میکند تا در فرآیندهای کورههای بلند به خوبی عمل کنند.
خواص شیمیایی
- آهن اسفنجی: آهن اسفنجی معمولاً دارای درصد بالای آهن خالص (90 تا 94 درصد) و مقادیر کمتری از ناخالصیها مانند سیلیسیم، منگنز و فسفر است. این ترکیب شیمیایی باعث میشود که آهن اسفنجی به عنوان یک ماده با کیفیت بالا برای تولید فولاد استفاده شود. آهن اسفنجی به دلیل فرآیند احیای مستقیم، خلوص بالاتری دارد و مقدار کمتری از آلودگیهای غیرآهنی را در بر میگیرد. این خلوص بالا باعث کاهش نیاز به تصفیههای اضافی در فرآیند تولید فولاد میشود.
- گندله: گندلهها معمولاً شامل ترکیب شیمیایی متنوعتری هستند که علاوه بر آهن، شامل مقادیر قابل توجهی از مواد افزودنی مانند بنتونیت (برای چسبندگی) میباشند. میزان آهن در گندلهها معمولاً کمتر از آهن اسفنجی است و میتواند بین 60 تا 70 درصد متغیر باشد. به دلیل فرآیند تولید و استفاده از مواد افزودنی، گندلهها ممکن است مقدار بیشتری از ناخالصیها را در خود داشته باشند. اما این ناخالصیها به طور کلی تأثیر زیادی بر عملکرد گندلهها در کورههای بلند نمیگذارند.
کاربردهای صنعتی آهن اسفنجی و گندله
در این بخش، به بررسی کاربردهای صنعتی آهن اسفنجی و گندله خواهیم پرداخت.
کاربردهای صنعتی آهن اسفنجی
- تولید فولاد در کورههای الکتریکی:
- آهن اسفنجی به طور عمده در تولید فولاد در کورههای الکتریکی (Electric Arc Furnace یا EAF) استفاده میشود. این کورهها برای تولید فولاد با کیفیت بالا و در مقادیر مختلف مناسب هستند. آهن اسفنجی به دلیل خلوص بالای خود، منبعی مناسب برای تولید فولاد با ویژگیهای مطلوب است.
- تولید آهن مایع برای کورههای بلند:
- در برخی از فرآیندهای تولید فولاد، آهن اسفنجی به عنوان ماده اولیه برای تولید آهن مایع در کورههای بلند (Blast Furnace) استفاده میشود. این فرآیند به کاهش مصرف سنگ آهن و افزایش بهرهوری در تولید فولاد کمک میکند.
- کاهش مصرف کک و انرژی:
- استفاده از آهن اسفنجی در فرآیند تولید فولاد میتواند به کاهش مصرف کک و انرژی کمک کند. این ماده، به دلیل ویژگیهای خاص خود، نیاز به تصفیههای کمتری دارد و باعث کاهش هزینههای تولید میشود.
- تولید فولاد ضد زنگ و آلیاژی:
- آهن اسفنجی به عنوان ماده اولیه در تولید فولادهای ویژه مانند فولادهای ضد زنگ و آلیاژی نیز استفاده میشود. این فولادها به دلیل ویژگیهای خاص خود، در صنایع مختلفی از جمله خودروسازی و صنایع نفت و گاز کاربرد دارند.
کاربردهای صنعتی گندله
- تولید فولاد در کورههای بلند:
- گندلهها به طور عمده در کورههای بلند (Blast Furnace) برای تولید فولاد استفاده میشوند. اندازه یکنواخت و خواص فیزیکی گندلهها باعث میشود که آنها به راحتی در کورههای بلند ذوب شوند و کیفیت فولاد تولیدی را بهبود دهند.
- تولید آهن خام (Pig Iron):
- گندلهها به عنوان ماده اولیه در تولید آهن خام در کورههای بلند مورد استفاده قرار میگیرند. آهن خام تولید شده میتواند برای تولید انواع مختلف فولادها و آلیاژها استفاده شود.
- کاهش آلودگی و افزایش بهرهوری:
- استفاده از گندلهها به دلیل یکنواختی در اندازه و ترکیب شیمیایی، میتواند به کاهش آلودگیهای زیستمحیطی و افزایش بهرهوری در کورههای بلند کمک کند. این ویژگیها باعث بهبود کیفیت هوای خروجی و کاهش هزینههای عملیاتی میشود.
- تولید فولاد با کیفیت بالا:
- گندلهها به دلیل فرآیند تولید خاص و خواص فیزیکی مناسب، در تولید فولادهای با کیفیت بالا کاربرد دارند. این فولادها به ویژه در صنایع ساختمانی، خودروسازی و تولید تجهیزات سنگین مورد استفاده قرار میگیرند.
مزایا و معایب آهن اسفنجی و گندله
برای انتخاب مناسبترین ماده اولیه در فرآیند تولید فولاد، بررسی مزایا و معایب هر کدام از مواد میتواند به تصمیمگیری بهتر کمک کند. در این بخش، جدول مزایا و معایب تفاوت آهن اسفنجی و گندله را بررسی میکنیم تا ویژگیهای کلیدی هر یک از این مواد را بهتر بشناسیم.
ویژگی | آهن اسفنجی | گندله |
---|---|---|
مزایا | ||
کیفیت بالای آهن | آهن اسفنجی دارای درصد بالای آهن خالص (90-94%) است که کیفیت فولاد تولیدی را بهبود میبخشد. | گندلهها نیز درصد آهن قابل قبولی دارند، اما کمتر از آهن اسفنجی است. |
کاهش مصرف انرژی | در مقایسه با فرآیندهای دیگر، آهن اسفنجی به دلیل فرآیند احیای مستقیم، مصرف انرژی کمتری دارد. | گندلهها به دلیل شکل و اندازه یکنواخت، باعث کاهش مصرف انرژی در کورههای بلند میشوند. |
کاهش آلودگی | استفاده از آهن اسفنجی میتواند به کاهش آلودگیهای محیطی کمک کند به دلیل کاهش نیاز به کک و مصرف کمتر انرژی. | گندلهها به دلیل فرآیند پخت، آلودگیهای کمتر و بهرهوری بالاتری دارند. |
قابلیت استفاده در کورههای الکتریکی | آهن اسفنجی به دلیل خلوص بالا و ویژگیهای مناسب، برای استفاده در کورههای الکتریکی فولادسازی ایدهآل است. | – |
معایب | ||
قیمت بالا | تولید آهن اسفنجی ممکن است به دلیل هزینههای احیای مستقیم و تجهیزات خاص، گرانتر باشد. | – |
حجم پایینتر و سختی زیاد | آهن اسفنجی به دلیل حجم پایینتر و سختی بیشتر، ممکن است مشکلاتی در حمل و نقل و ذخیرهسازی ایجاد کند. | – |
نیاز به فرآیند پیشرفته | فرآیند احیای مستقیم نیاز به تجهیزات پیشرفته و هزینهبر دارد. | – |
پخت و زمان تولید | – | فرآیند تولید گندله شامل مرحله پخت و زمان تولید بیشتری است که میتواند هزینهها را افزایش دهد. |
تولید گندلههای با کیفیت پایین | – | گندلهها ممکن است دارای کیفیتهای متغیری باشند و نیاز به کنترل دقیقتر در فرآیند تولید دارند. |
نیاز به مواد افزودنی | – | تولید گندلهها نیاز به مواد افزودنی مانند بنتونیت دارد که میتواند بر هزینهها و ترکیب شیمیایی تأثیر بگذارد. |
هر کدام از آهن اسفنجی و گندله مزایا و معایب خاص خود را دارند که بر انتخاب آنها در فرآیند تولید فولاد تأثیر میگذارد. آهن اسفنجی به دلیل خلوص بالا و مصرف انرژی کمتر، برای کورههای الکتریکی مناسب است، در حالی که گندلهها به دلیل شکل یکنواخت و کاهش آلودگی، برای کورههای بلند مورد استفاده قرار میگیرند. در نهایت، انتخاب مناسب بین این دو ماده بستگی به نیازهای خاص تولید فولاد، نوع کوره و هزینههای مربوطه دارد.
نسبت تبدیل گندله به آهن اسفنجی
در فرآیند تولید فولاد، گندلهها و آهن اسفنجی به عنوان مواد اولیه مورد استفاده قرار میگیرند. یکی از جنبههای مهم در این فرآیند، نسبت تبدیل گندله به آهن اسفنجی است. این نسبت نشاندهنده میزان تبدیل گندلهها به آهن اسفنجی در طی فرآیند احیا است و تأثیر زیادی بر بهرهوری و هزینههای تولید دارد. در این بخش، به بررسی نسبت تبدیل گندله به آهن اسفنجی و عوامل مؤثر بر آن خواهیم پرداخت.
فرآیند تبدیل گندله به آهن اسفنجی معمولاً در کورههای احیای مستقیم (Direct Reduction Furnace یا DRF) انجام میشود. در این فرآیند، گندلهها به همراه یک عامل احیا (مانند گاز طبیعی یا کربن) در دمای بالا قرار میگیرند تا آهن موجود در گندلهها احیا شده و به صورت آهن اسفنجی درآید.نسبت تبدیل گندله به آهن اسفنجی به میزان آهن موجود در گندلهها و راندمان فرآیند احیا بستگی دارد. معمولاً این نسبت به صورت درصد بیان میشود و نشاندهنده درصد گندلههایی است که به آهن اسفنجی تبدیل میشود.به طور کلی، نسبت تبدیل گندله به آهن اسفنجی معمولاً بین 80 تا 90 درصد متغیر است. این به این معنی است که از هر 100 کیلوگرم گندله، 80 تا 90 کیلوگرم آن به آهن اسفنجی تبدیل میشود.
عوامل مؤثر بر نسبت تبدیل
کیفیت گندلهها، از جمله اندازه و ترکیب شیمیایی، بر نسبت تبدیل تأثیر میگذارد. گندلههای با کیفیت بالا که به خوبی پخته شدهاند و درصد آهن بالایی دارند، معمولاً نسبت تبدیل بهتری دارند.شرایط فرآیند احیا، از جمله دما، فشار و نوع عامل احیا، بر نسبت تبدیل گندله به آهن اسفنجی تأثیر میگذارد. کنترل دقیق این شرایط میتواند به بهبود نسبت تبدیل کمک کند.ترکیب شیمیایی گندلهها، از جمله میزان ناخالصیها و مواد افزودنی، میتواند بر راندمان فرآیند احیا و نسبت تبدیل تأثیر بگذارد. گندلههایی که دارای درصد کمتری از ناخالصیها هستند، معمولاً نسبت تبدیل بهتری دارند.طراحی و بهرهوری کوره احیا نیز بر نسبت تبدیل تأثیرگذار است. کورههای مدرن و بهینهسازی شده میتوانند نسبت تبدیل بالاتری را فراهم کنند.
نتیجهگیری نهایی: تفاوت آهن اسفنجی و گندله
انتخاب بین آهن اسفنجی و گندله بستگی به نیازهای خاص تولید فولاد، نوع کوره، هزینهها، و اهداف کیفیت دارد. آهن اسفنجی با ویژگیهای خود در کاهش مصرف انرژی و تولید فولاد با کیفیت بالا، در کورههای الکتریکی برتری دارد. از سوی دیگر، گندلهها با شکل یکنواخت و بهبود بهرهوری در کورههای بلند، انتخاب مناسبی برای تولید در این کورهها هستند. تحلیل دقیق این عوامل و نیازهای خاص فرآیند تولید، میتواند به انتخاب بهینه و کارآمدترین ماده اولیه کمک کند.در این مقاله، به بررسی کلی تفاوت آهن اسفنجی و گندله پرداخته و نحوه تولید، نسبت تبدیل گندله به آهن اسفنجی و کاربردهای آنها را شرح دادیم.