آهن اسفنجی چیست؟ مزایا و کاربرد استفاده
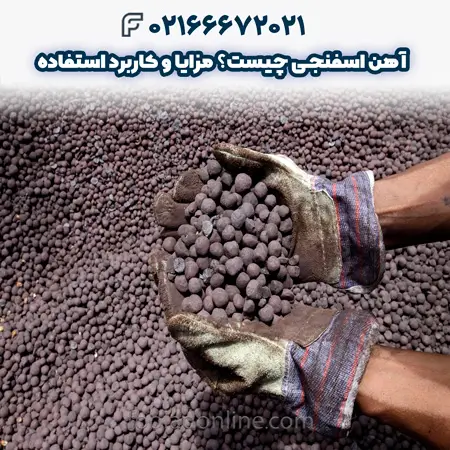
آهن اسفنجی، که به نامهای DRI (Direct Reduced Iron) یا HBI (Hot Briquetted Iron) نیز شناخته میشود، یک محصول واسطهای در تولید فولاد است که از احیای مستقیم سنگ آهن در حالت جامد به دست میآید. این فرآیند، که به احیای مستقیم معروف است، از گازهای احیا کننده مانند هیدروژن و مونوکسید کربن برای کاهش اکسید آهن به آهن فلزی استفاده میکند، بدون اینکه مرحله ذوب را طی کند.در ادامه این مقاله، به بررسی دقیقتر فرآیند تولید، کاربردها، مزایا و چالشهای مرتبط با آهن اسفنجی خواهیم پرداخت و همچنین نگاهی به به بررسی آهن اسفنجی چیست، راکتور احیای آهن اسفنجی چیست، ریمیت آهن اسفنجی چیست، لجن آهن اسفنجی چیست و بریکت آهن اسفنجی چیست خواهیم انداخت.
آهن اسفنجی به دلیل داشتن خلوص بالا و کمبود عناصر آلیاژی مانند کربن، سیلیکون، منگنز، و فسفر، یک ماده اولیه مطلوب برای تولید فولاد با کیفیت بالا است. همچنین، این روش تولید، به دلیل کاهش انتشار گازهای گلخانهای و مصرف انرژی پایینتر نسبت به فرآیند کوره بلند، به عنوان یک روش سازگار با محیط زیست شناخته شده است.
تاریخچه آهن اسفنجی: از گذشته تا کنون
تاریخچه آهن اسفنجی به دوران باستان بازمیگردد، جایی که اولین روشهای به دست آوردن آهن از سنگ معدن در خاورمیانه و اروپا مورد استفاده قرار میگرفت. این روشها، که حداقل تا سده شانزدهم میلادی رایج بودند، از فرآیندهای احیای مستقیم برای تولید آهن استفاده میکردند.
در این فرآیندها، سنگ آهن در دمای بالا و در حضور گازهای احیا کننده مانند هیدروژن و مونوکسید کربن قرار میگرفت تا اکسیژن آن کاهش یابد و آهن فلزی تولید شود. این روش، که به دلیل تولید آهن با خلوص بالا و کمبود عناصر آلیاژی مطلوب بود، به نام آهن اسفنجی شناخته شد.
در دهه ۱۹۶۰، با پیشرفتهای صنعتی، ایده احیای مستقیم آهن اسفنجی به روشهای جدیدتر و کارآمدتر توسعه یافت. اولین کارخانه آزمایشی احیای مستقیم آهن اسفنجی به روش میدرکس در سال ۱۹۶۷ در تولدو، اوهایو ساخته شد و اولین کارخانه تجاری با ظرفیت تولید ۱۵۰ هزار تن در سال ۱۹۶۹ در پورتلند، اورگون افتتاح گردید.
از آن زمان تاکنون، تکنولوژی تولید آهن اسفنجی به طور چشمگیری پیشرفت کرده و در بسیاری از کشورها به عنوان یک روش مطلوب و محیط زیستی برای تولید آهن و فولاد مورد استفاده قرار گرفته است. در ایران نیز، استفاده از آهن اسفنجی در کورههای القایی از سال ۱۳۸۹ آغاز شده و به تدریج به عنوان یک جایگزین مناسب برای ضایعات آهن در فرایند ذوب مورد توجه قرار گرفته است.
راکتور احیای آهن اسفنجی چیست؟
در جواب به سوال راکتور احیای آهن اسفنجی چیست باید بگوییم که راکتور احیای آهن اسفنجی، که به نام DRI (Direct Reduced Iron) نیز شناخته میشود، یک کوره صنعتی است که در فرآیند احیای مستقیم سنگ آهن برای تولید آهن اسفنجی کاربرد دارد. این فرآیند در دماهایی پایینتر از نقطه ذوب آهن رخ داده و شامل کاهش اکسیدهای آهن (به شکل توده، گلوله یا پودر) به آهن فلزی با استفاده از گاز احیاکننده است.
گاز احیاکننده میتواند مخلوطی از هیدروژن و منوکسید کربن (گاز سنتز) یا هیدروژن خالص باشد. اصطلاح “آهن اسفنجی” از بافت متخلخل و شبیه به اسفنج آهن پس از فرآیند احیا گرفته شده است. راکتور در حالت جامد عمل میکند، به این معنی که آهن در طی فرآیند احیا ذوب نمیشود. این روش از نظر انرژی کارآمد بوده و امکان تولید آهن بدون نیاز به کوره بلند سنتی را فراهم میکند.
آهن اسفنجی حاصل شده میتواند به عنوان ماده اولیه برای کورههای قوس الکتریکی در صنعت فولادسازی، به ویژه در کارخانههای کوچک که از قراضه با کیفیت پایین استفاده میکنند یا فولاد با کیفیت بالاتر تولید میکنند، مورد استفاده قرار گیرد. در ادامه به بررسی و پاسخ سوال ریمیت آهن اسفنجی چیست میپردازیم.
ریمیت آهن اسفنجی چیست؟
ریمیت آهن اسفنجی، فراوردهای است که از احیای مستقیم سنگ آهن حاصل میشود و به دلیل داشتن خلوص بالای آهن و کمبود ناخالصیها، به عنوان یک جایگزین مناسب برای ضایعات آهن در صنایع فولادسازی مورد استفاده قرار میگیرد. این ماده به شکل گلولهای یا کلوخهای شکل و متخلخل است و معمولاً از آهن با عیار 67 درصد تولید میشود.
ریمیت آهن اسفنجی در فرآیند فولادسازی ذوب شده و برای تولید انواع شمش آهن، میلگرد و اسلب استفاده میگردد. استفاده از این ماده در مقایسه با ضایعات و قراضههای آهن باعث افزایش چشمگیر کیفیت و عیار فولاد تولید شده میشود. همچنین، فولاد تولید شده با استفاده از ریمیت آهن اسفنجی، استحکام و مقاومت بیشتری دارد.
مزایای استفاده از ریمیت آهن اسفنجی چیست ؟ این آهن با داشتن درصد خلوص آهن بالاتر نسبت به قراضه آهن، مصرف انرژی و آب کمتر در زمان ذوب، و کیفیت بالاتر محصولات نهایی است. با این حال، ریمیت آهن اسفنجی در مقایسه با فولاد ممکن است سریعتر دچار فرسایش و زنگزدگی شود، که این مسئله یکی از معایب این ماده است. در ادامه به بررسی لجن آهن اسفنجی چیست میپردازیم.
لجن آهن اسفنجی چیست؟
در جواب به سوال لجن آهن اسفنجی چیست باید بگوییم که لجن آهن اسفنجی یکی از فرآوردههای جانبی حاصل از فرآیند تولید آهن اسفنجی است. این ماده به صورت پودری و متشکل از مخلوطی از مواد معدنی اصلی مانند آهن، سیلیس، آلومینا، کلسیم، منیزیم و سایر عناصر دیده میشود. لجن آهن اسفنجی معمولاً در نتیجه فرآیندهای جداسازی و تصفیه در کارخانههای تولید آهن اسفنجی به دست میآید و میتواند حاوی مقادیر قابل توجهی از آهن باشد.
به دلیل داشتن مواد معدنی مفید، لجن آهن اسفنجی میتواند در کاربردهای مختلفی مورد استفاده قرار گیرد. برخی از کاربردهای احتمالی آن شامل تولید سیمان، به عنوان افزودنی در خاکهای کشاورزی برای بهبود محتوای مواد مغذی، و یا در صنایع سرامیک به عنوان ماده اولیه است. با این حال، استفاده از لجن آهن اسفنجی نیازمند فرآیندهای پیشرفته تصفیه و بازیافت است تا اطمینان حاصل شود که مواد زائد و ناخالصیها به حداقل رسیده و محصول نهایی برای کاربرد مورد نظر مناسب باشد.
بریکت آهن اسفنجی چیست؟
بریکت آهن اسفنجی، که به عنوان Direct Reduced Iron (DRI) نیز شناخته میشود، یک فرآورده نوین در صنعت فولاد است که از فناوریهای پیشرفته در صنعت فلزی تولید میشود. بریکت، نسخه بهبود یافتهای از آهن اسفنجی است که در فرآیند بریکتسازی تولید میشود. در این فرآیند، آهن اسفنجی را در دمای مناسب فشردهسازی و به شکل قطعههای فشرده تبدیل میکنند.
انواع بریکت آهن اسفنجی چیست
فرآیند بریکت آهن اسفنجی چیست ؟ این فرایند به دو دسته بریکتسازی سرد (CBI) و بریکتسازی گرم (HBI) تقسیم میشود:
- بریکت سرد (CBI): در این روش، مواد ورودی در دمای محیط به ماشین بریکتزنی منتقل میشوند و دو نوع بریکت تولید میشود.
- بریکت گرم (HBI): این نوع بریکت با استفاده از آهن اسفنجی گرم (HDRI) در دمای بالاتر از 650 درجه سانتیگراد ساخته میشود.
مزایای استفاده از بریکت آهن اسفنجی چیست ؟
استفاده از بریکت آهن اسفنجی در صنعت فولادسازی مزایای بسیاری دارد، از جمله:
- افزایش کیفیت بار فلزی: استفاده از بریکت آهن اسفنجی منجر به بهبود کیفیت بار فلزی و افزایش مقاومت و خواص مکانیکی فولاد تولید شده میشود.
- کاهش مصرف کک: استفاده از بریکت در کورههای بلند منجر به کاهش مصرف سوخت کک و بهبود بهرهوری و کاهش هزینههای تولید میشود.
- جایگزینی قراضه: در کورههای القایی و قوس الکتریکی، بریکت میتواند قراضه را جایگزین کند، که این باعث کاهش هدررفت انرژی و استفاده بهینه از منابع انرژی میشود.
فرآیند تولید آهن اسفنجی: مراحل و روشها
تولید آهن اسفنجی یکی از مهمترین فرآیندهای صنعتی در صنایع فولاد است که از احیای مستقیم سنگ آهن در حالت جامد به دست میآید. این فرآیند شامل چندین مرحله کلیدی است که به ترتیب زیر انجام میشو:
- تهیه مواد اولیه: ابتدا، سنگ آهن پس از استخراج، کنسانتره شده و به گُندِله تبدیل میشود.
- گندلهسازی: گندلههای سنگ آهن با عیار 67 درصد تولید شده و در مرحله بعدی پخته میشوند.
- گرمایش: مواد آماده شده در کوره دوار وارد شده و توسط سیستم مشعل گرم میشوند، دمای کوره بین 1100 تا 1200 درجه سانتیگراد است.
- کاهش: در کوره، واکنشهای شیمیایی انجام میشود که باعث احیای اکسید آهن (Fe2O3) موجود در سنگ آهن و تبدیل آن به فلز آهن میشود.
- خنکسازی: پس از خروج آهن از کوره، آن را با استفاده از هوا یا آب خنک میکنند تا از اکسیداسیون مجدد آن جلوگیری شود.
- غربالگری: آهن اسفنجی تولید شده غربال شده و ذرات بزرگ یا ناخالصیها جدا میشوند.
- بریکتسازی یا گندلهسازی: آهن اسفنجی به فرم مورد نیاز محصول نهایی، مانند بریکت یا گندله، تبدیل میشود.
این فرآیند به دلیل کارآمدی انرژی و تولید آهن با خلوص بالا، به عنوان یک روش مطلوب در صنعت فولادسازی شناخته شده است. آهن اسفنجی تولید شده میتواند به عنوان ماده اولیه در کورههای قوس الکتریکی یا برای تولید فولاد با کیفیت بالا استفاده شود.
انواع روشهای احیای مستقیم: میدرکس، HYL و…
در صنعت فولادسازی، احیای مستقیم به عنوان یک روش نوین برای تولید آهن اسفنجی از سنگ آهن مطرح است. این روشها به دلیل کاهش هزینهها و اثرات مخرب محیطی نسبت به روشهای سنتی، مورد توجه قرار گرفتهاند. در ادامه، به بررسی دو روش رایج و متداول احیای مستقیم میپردازیم.
روش میدرکس (Midrex)
روش میدرکس یکی از پربازدهترین روشهای تولید آهن اسفنجی است. در این روش، از گاز طبیعی به عنوان احیاکننده استفاده میشود. فرایند شامل آسیاب شدن سنگ آهن به صورت گندله و ورود آن به کوره به همراه متان است. متان در رفورمرها تجزیه شده و به هیدروژن و منوکسید کربن تبدیل میشود، که سپس برای احیای سنگ آهن به کار میروند.
روش HYL
روش HYL نیز مشابه روش میدرکس است و از گاز طبیعی به عنوان احیاکننده استفاده میکند. تفاوت اصلی در فرایند تولید هیدروژن است؛ در روش HYL، هیدروژن از شکست متان با بخار آب در دمای بالا تولید میشود.
سایر روشها
علاوه بر میدرکس و HYL، روشهای دیگری نیز وجود دارند که بر اساس منابع انرژی موجود و نیازهای خاص هر کارخانه توسعه یافتهاند. این روشها میتوانند شامل استفاده از زغال سنگ به جای گاز طبیعی یا ترکیبی از هر دو باشند.
کاربردهای آهن اسفنجی در صنعت: از فولادسازی تا…
آهن اسفنجی، که به عنوان DRI (Direct Reduced Iron) نیز شناخته میشود، یکی از مهمترین مواد اولیه در صنعت فولادسازی است. این ماده به دلیل داشتن عیار بالای آهن و کمبود ناخالصیها، کاربردهای گستردهای دارد.
در صنعت فولادسازی
- تولید فولاد: آهن اسفنجی به طور گستردهای برای تولید فولاد در کورههای قوس الکتریکی و کورههای القایی استفاده میشود. این ماده میتواند تا ۵۰ درصد قراضه را در فرآیند تولید فولاد جایگزین کند.
- تولید میلههای TMT: آهن اسفنجی برای تولید میلههای TMT با کیفیت بالا استفاده میشود که در ساختمانسازی و پروژههای عمرانی کاربرد دارند.
- تولید لولههای DI: لولههای DI که در سیستمهای لولهکشی و انتقال آب به کار میروند، از آهن اسفنجی تولید میشوند.
در سایر صنایع
- ریختهگری: آهن اسفنجی در ریختهگری برای تولید بیلت، اسلب و میلگرد استفاده میشود.
- تولید آهن فرفورژه: آهن اسفنجی در تولید آهن فرفورژه یا فولاد فرآوریشده کاربرد دارد.
مزایای استفاده از آهن اسفنجی
- کاهش آلودگی: استفاده از آهن اسفنجی به کاهش آلودگیهای زیستمحیطی کمک میکند.
- افزایش کیفیت: آهن اسفنجی به دلیل خلوص بالا، به افزایش کیفیت محصولات فولادی منجر میشود.
- کارایی انرژی: استفاده از آهن اسفنجی در فرآیندهای تولید فولاد، مصرف انرژی را کاهش میدهد.
مطالعه موردی: تولید آهن اسفنجی در ایران
ایران به عنوان یکی از بزرگترین تولیدکنندگان آهن اسفنجی در جهان شناخته شده است. با توجه به دسترسی به منابع غنی سنگ آهن و گاز طبیعی، ایران توانسته است در تولید آهن اسفنجی به وسیله فرآیند احیای مستقیم (DRI) پیشرفتهای چشمگیری داشته باشد.
پیشرفتها و دستاوردها
- افزایش تولید: ایران در سالهای اخیر توانسته است تولید آهن اسفنجی خود را به طور قابل توجهی افزایش دهد. به گزارش انجمن تولیدکنندگان فولاد ایران، تولید آهن اسفنجی در سال ۱۴۰۱ به بیش از ۳۰ میلیون تن رسیده است، که نسبت به سال گذشته رشد ۹.۱ درصدی داشته است.
- رتبه برتر در تولید: ایران در سال ۲۰۲۰ دومین تولیدکننده بزرگ آهن اسفنجی در جهان بوده و این جایگاه را با فاصله چشمگیر از دیگر کشورها حفظ کرده است.
چالشها و راهکارها
- محدودیتهای انرژی: با وجود محدودیتهای اخیر در مصرف گاز، کارخانههای تولید آهن اسفنجی با چالشهایی مواجه شدهاند. این محدودیتها میتواند بر تولید و صادرات آهن اسفنجی تأثیر بگذارد.
- بهبود فرآیندها: برای مقابله با این چالشها، تولیدکنندگان به دنبال بهبود فرآیندهای تولید و استفاده از فناوریهای نوین هستند تا بتوانند با کاهش مصرف انرژی، تولید خود را حفظ و توسعه دهند.
تولید آهن اسفنجی در ایران نمونهای از توانمندیهای صنعتی کشور در بهرهبرداری از منابع طبیعی و تبدیل آنها به محصولات با ارزش افزوده بالا است. با وجود چالشهای پیش رو، ایران همچنان به عنوان یک بازیگر کلیدی در عرصه تولید آهن اسفنجی در سطح جهانی باقی مانده است. در این مقاله به بررسی آهن اسفنجی چیست، راکتور احیای آهن اسفنجی چیست، ریمیت آهن اسفنجی چیست، لجن آهن اسفنجی چیست و بریکت آهن اسفنجی چیست پرداختیم.